Revolutionary Manufacturing Breakthrough: How Engineers Slashed Aircraft Door Production Time
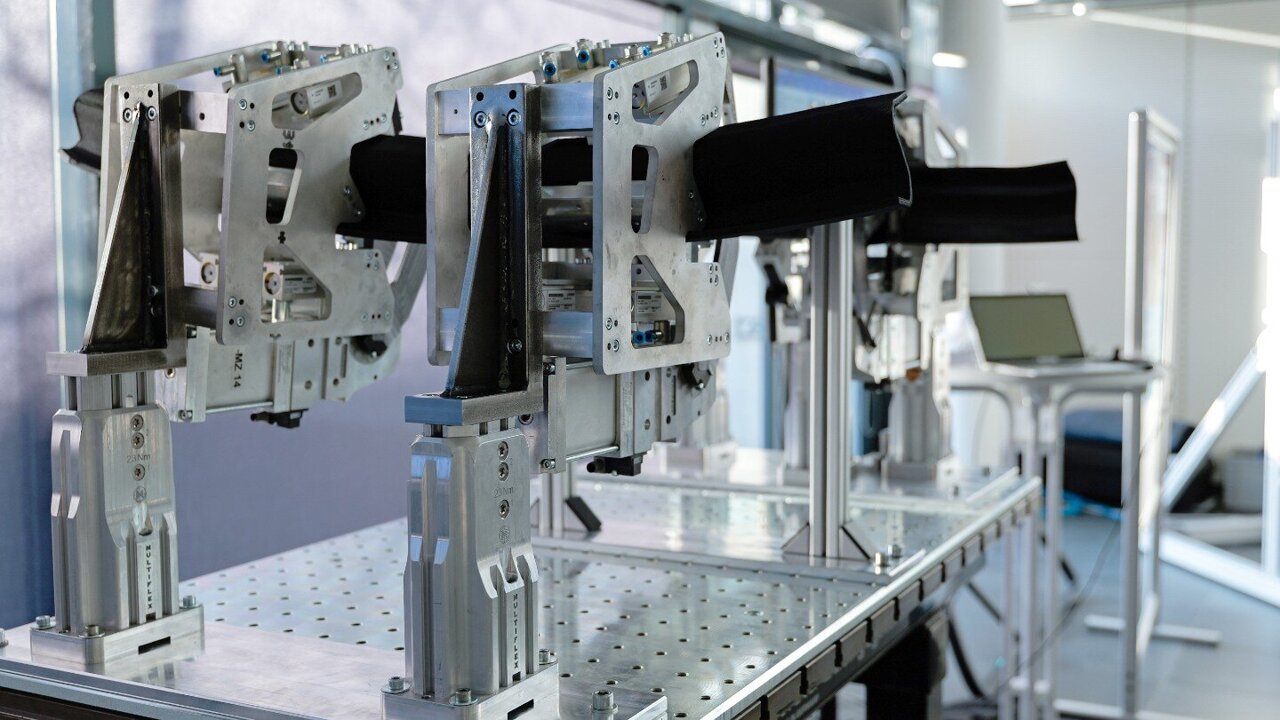
In the intricate world of aerospace manufacturing, passenger aircraft doors remain a testament to traditional craftsmanship. Despite rapid technological advancements, these critical components are still predominantly crafted through meticulous manual labor. The most labor-intensive phase of door production involves the painstaking process of assembling complex door structures using an array of screws and rivets.
Each door represents a symphony of precision, requiring numerous intricate steps to ensure structural integrity and passenger safety. Skilled technicians carefully align, position, and secure each component, transforming raw materials into robust, reliable aircraft entryways. The manual approach, while time-consuming, allows for unparalleled attention to detail and quality control that automated processes might overlook.
This blend of human expertise and engineering excellence continues to define the aerospace manufacturing landscape, highlighting the irreplaceable role of skilled craftspeople in creating the sophisticated components that enable modern air travel.